The MPS Process - Page 2
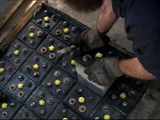
Once the tray's lining has been applied, we stow the good rebuild or brand-new cells in the tray.
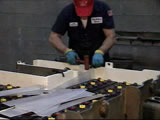
Acid-resistant plastic shimmies are hammered between cells to ensure a snug fit. Then a rop-like warming compound is placed between cells.
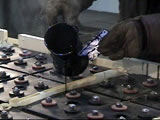
We apply asphalt to the top of the battey to seal it off from acid seepage and other debris. The warming compound prevents the asphalt from seeping down between the cells and bonding them together.
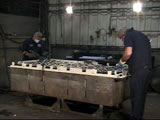
We then burn on the lead connectors.
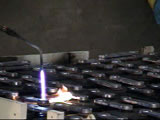
The asphalt seal is "flamed" to ensure its integrity.
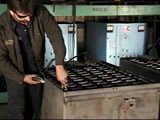
On rebuilds, we give the battery another round of Pluskota charging and load banking. We do this because cellls that gave good readings can be damaged during the process of removal from the tray. This exit load band is in place so that we are sure of the quality of the cells we are returning to customers.
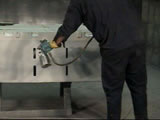
We tape off the top of the battery and paint the tray with a minimum of six coats of acid-resistant paint.
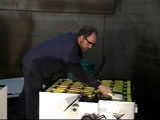
The battery has its decals applied and gets washing with a chemical detergent or baking soda solution. A final inspection is made of the battery.
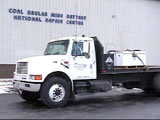
The good-as-new battery goes out for delivery!
Click here to go to the previous page