The MPS Process - Page 1
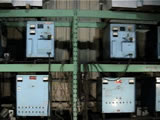
First, we charge your battery to its full capacity with a Pluskota Variable Voltage Regulated Charger. The VVR gives a trickle charge over a 24-48 hour period. This keeps the battery cool and helps to break up sulfation in the battery's cell plates. The charging process helps us to accurately assess what kind of life a battery's cells have left.
Then, we connect the battery to a Pluskota Load Bank which simulates the battery's normal load in its machine. It is tested over a 4-6 hour period at either 80 or 100 percent capacity.
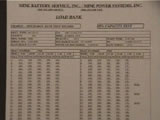
We notate the information garnered in the testing processo n the sheet shown here and forward it to the customer so that he may see the state of his cells. We also send an estimate for rebuild or retray as well as a letter containing our recommendation on which way to go.
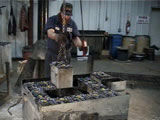
After we get the go ahead for rebuild or retray, we disassemble the battery. we drill off the connectors and pull the cells from the tray.
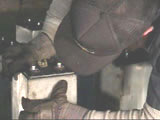
We clean the cells of tar and check their heat seals. They then go on pallets while we turn our attention to refurbishing the tray.
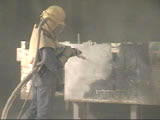
First, we sandblast the tray down to bare metal using eith black beauty or steel grit.
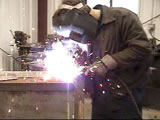
Then, we transport it to our welding room where any structural flaws are corrected.
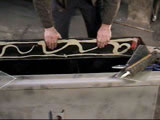
Next, trays receive one of two linings. These are important because they help to prevent electrical ground from forming between the battey's cells and its steel tray. When a ground forms, the battery will not charge properly and over time will lose capacity. Shown here is a fiberglass lining which is cut in 6-8 inch strips and glued on the inside of the tray with liquid nails. This is a low-cost option.
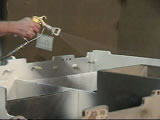
We also offer Plastisol as a lining. This poly-vinyl-chloride compound is acid, heat and voltage resistant. It requires a primer to bind to steel and we apply it with a minimum of 30 ML build.
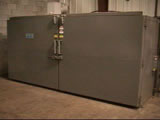
We then bake it at 300 degrees for 1-1/2 hours. We are the only rebuild shop in the country with plastisol capabilities.
Click here for the next page